Wind power may seem eco-friendly, but with most sails essentially made from plastic, it’s time for greener technology, says Sam Fortescue
Eco sails: options for sustainable sails
Sailing is a conundrum to me sometimes. We all love to slip the lines, with the cares and worries that go with life ashore, and surround ourselves with the majesty of a good seascape.
We wax lyrical about weather and wildlife, yet how often do we sigh crossly then fire up the engine for a knot or two more pace?
And how much do we covet new gadgets and doodahs to fill up our boats?
Sails encapsulate this contradiction nicely for me.
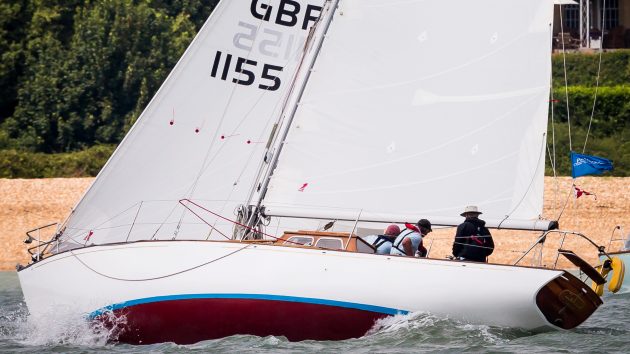
Dacron is a long-standing mainstay of cruising and racing sails. Credit: Guido Cantini / seasee.com
On the one hand they are the sustainable motors of our boats, turning wind into motion.
They provide a constant challenge – willing us to trim and tweak for a slightly better aerofoil and a fraction of a knot more speed.
On the other hand, they represent nothing more or less than a huge sheet of plastic or, even worse, carbon fibre.
Eco Sails: Upcycling
We rarely think about it, but where do these materials come from, and what happens to a sail when it’s too worn or too baggy to do its job properly?
Well, a few of the more colourful ones get sent for upcycling into not-very-waterproof tote bags or jackets.
That’s the story of Salcombe’s Quba & Co and a host of smaller brands and start-ups.
Before you turn the page thinking ‘that’s sorted then’, bear in mind that very, very few sails are recycled in this way.
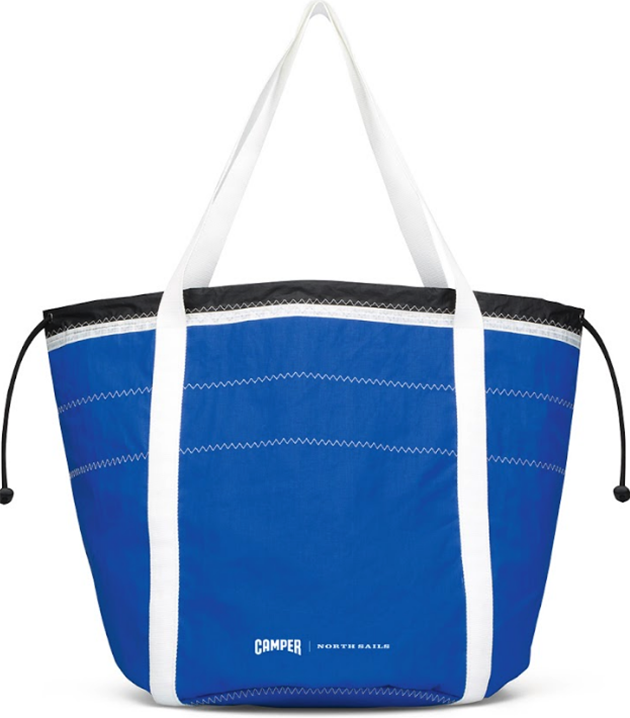
Although upcycling sails is a worthy option, it only takes a few sails
As Peter Kay of One Sails UK tells me: ‘It’s a nice idea, but there’s a limit to how many of those the world needs.’
Three sails will keep a small operator busy for months, while big brands with more industrial production lines find worn sails hard to deal with.
‘I remember quoting for making distressed sails for one brand – putting it through a garment manufacturing process that makes it look used,’ Kay adds.
All the same, North Sails still sees upcycling as a useful medium-term way of taking sails out of waste streams.
And in fact, it is planning to announce a much larger scale operation soon.
‘Stay tuned on the bags argument,’ says North’s woven sails expert Tom Davis. ‘Repurposing at scale is the best solution to divert sails out of landfill.’
Eco Sails: Recycling
OneSails does have another solution, however. If you buy its top-of-the-line Forte 4T, made with continuous yarn composite construction, they are ISO certified to be recyclable.
Because these are made without glue or Mylar film, they are pure polyester and can be processed at an existing recycling plant back into PE pellets for further use.
‘You just go to the factory that does other sorts of processing of other sorts of polyethylene,’ explains Kay. ‘It’s the same process Tesco uses to recycle old poly bags.’
Well, hold on a second. The general public isn’t usually encouraged to trundle off to industrial recycling plants with an old sail and a few plastic bags – a fact that Kay concedes.
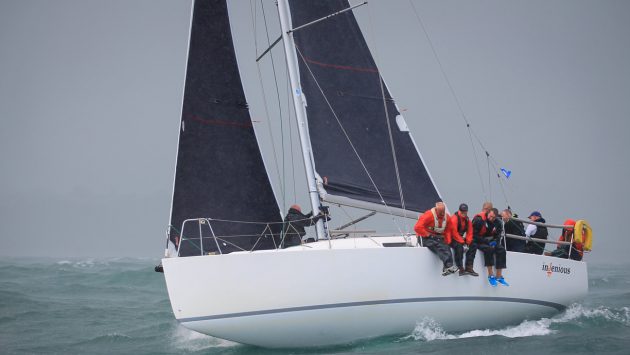
One Sails’ Forte 4T sails are made from a single material, making them more easily recyclable. Credit: Green Sea Photography
‘The next part of the jigsaw is to have the infrastructure that would allow us to take sails back, get them into a big enough commercial skip size that we
can then commercially give it to the recycling plant,’ he says.
‘We’re getting closer, but I can’t claim that we’re at the point now where you can do it.’
So, the sails can be recycled, but are not currently being returned in sufficient volume for a dedicated OneSails collection system to have been set up.
Forte 4T was only introduced five years ago, so not many have reached the end of their lives.
In the meantime, Kay says that OneSails lofts should be able to store end-of-life sails until there are enough for a trip to the recycling plant.
The German Boatbuilders’ Association (DBSV) has taken its own steps forward on this, with the launch of the Cleen Sailing Initiative.
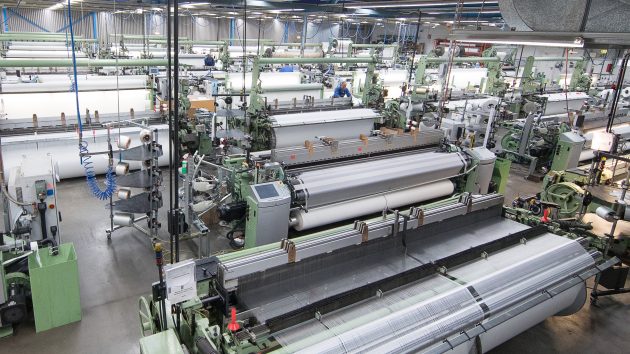
Dimension Polyant in Germany is one of the leading manufacturers of sail cloth in Europe and is aiming to make more of its products and processes carbon neutral. Creidt: Fotografie C.B
Its members have signed up to a traffic-light system so that customers can judge for themselves how sustainable each brand is.
And in order for a new sail to wear the ‘Cleen’ badge, the sailmaker must have collected and recycled a corresponding old sail.
This is a national solution, and sailcloth maker Dimension Polyant believes that that’s the way recycling should work – in small cells, not global networks.
‘The biggest task the industry needs to find a solution for is to convince sailors to give their old sails back to the system and to build such a system in the first place,’ says general manager Uwe Stein.
‘It does not make sense to carry the sails around the whole world, we need to find local partners.’
Under the Cleen Sailing Initiative, the system must be up and running in early 2022.
Eco Sails: Mixed materials
But part of the problem with everyday Dacron-style polyester sails is that they are not made of one single material and are not suitable for existing waste streams.
A woven sail first has to be stripped of battens and sail hardware – a moderately time-consuming process in its own right.
Then any glue, tape and the resin coating that woven cloth is typically finished with has to be removed.
‘The process won’t allow other chemicals in the recycling process,’ says Elvstrøm Sails’ R&D manager Flemming Christensen. ‘This separation is a very ineffective and expensive process, but the industry is working on optimising it.’
Continues below…
Expert advice: sails and rigging
Sails and rigging are the engine room of any sailing boat from small dinghies up to giant superyachts. No matter…
10 tips to make your sails last longer
Professional skipper Simon Phillips shares his tips on how to get better value from your sails
How to reef to sail safely through any weather
Pete Goss delivers his masterclass on when to reef, and explains why it is critical to keeping control of your…
Boat building: what will yachts be made from in the future?
Sam Fortescue shines a light on boat building jargon and looks into a future devoid of fibreglass
North in fact did some work with a Japanese yarn supplier 10 years ago to look at just this issue.
They found that it was possible, technically at least, and there is 36-footer sailing in French waters using a suit of sails entirely sourced from recycled polyester.
‘They found a method to break down old sailcloth chemically, then re-spin it,’ says Davis. ‘But it’s probably the world’s most expensive suit of sails.’
Not repeatable at scale, then.
Supply chains
But perhaps we’re also looking at the problem from the wrong end. From the oil refinery to the sail loft, there’s a huge and complex supply chain that also has a carbon footprint.
This is mainly the domain of the cloth weavers, yarn makers and film manufacturers.
And as most of the world’s sailcloth comes from four big companies, there is surely plenty of commercial clout for research and development.
Surprisingly, given the growing intensity of the environmental debate over recent decades, the question of yarns made from recycled plastic seems to have begun fairly recently.
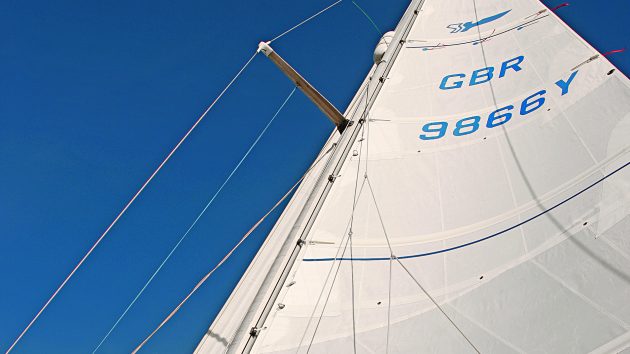
Premium cruising sails can now be made with bio-based Hydranet cloth
‘We are doing a lot of research on this with our suppliers,’ says Uwe Stein of Dimension-Polyant. ‘We are currently doing tests with different fibres and yarns, but to be honest, we are not happy with the results yet. The only fibre that offers the same performance, even though it comes from bio-based materials, is Dyneema.’
That’s why Dimension has recently launched a new bio-based version of its Hydra Net radial sailcloth – the best-selling cloth made with Dyneema.
It goes a step further by badging it as CleenTEC climate-neutral sailcloth, thanks to the use of green electricity and emissions off-setting.
‘We are proud to be able to offer our sailmakers our first completely climate-neutral sailcloth, which also saves fossil raw materials,’ says Stein.
Recycled material
But what about the cheaper end of the market, overwhelmingly represented by woven polyester sailcloth, such as Dacron?
That is what most of us use for cruising sailing.
Well, yarn made from old plastic bottles is already a reality. Both polyester and nylon from 100% recycled PET is available today.
US manufacturer Repreve processes 2.2 billion plastic bottles every year into 75m lbs (34,000 tonnes) of fibre, some of which gets transformed into sailcloth by Challenge.
None of the sailmakers I spoke to are willing to touch it, though.
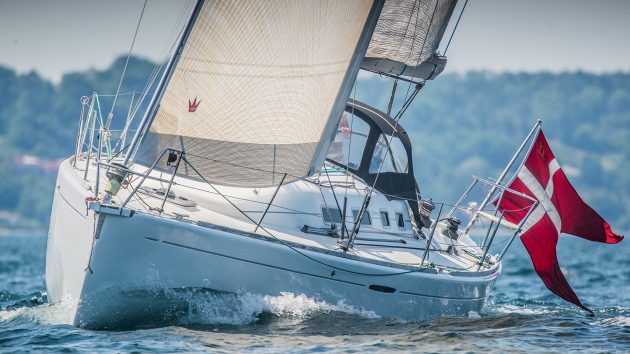
Eco sails: Elvstrom EPEX Ekko sails use taffeta, UV film and fibre that all come from recycled sources. Credit: Nikola J Schwaner
Nobody was prepared to go into brand specifics, but they all said that there was still nothing which met their quality standards.
‘Dacron is a really special kind of polyester yarn – it’s not the same as what’s in your socks,’ explains North’s Davis.
‘It is continuous filament, high tenacity and high shrink – those three things together are the secret to making high-quality, plain weave Dacron sailcloth. If you don’t have them, you can make something that looks like sailcloth, but it won’t perform like it.’
Denmark’s Elvstrøm Sails is actively working on this approach.
‘We are investigating the process of making PET-woven cloth from PET-recycled scrap (bottles),’ says Christensen. ‘Theoretically it is possible. Some
woven PET already exists, but until now, not for this industry.’
There has been more success on the laminate side, however.
Elvstrøm has an exclusive tie-up with Challenge to offer a sail using fibre, taffeta and UV film that all comes from recycled content.
The laminate bears the loft’s ‘Ekko’ sustainability mark.
A blend of black polyester and high modulus ultra-PE held together with solvent- free glues, gives the finished sail a grey look. And the best part?
It costs the same as other laminates sourced from virgin material.
Further up the performance curve is the Danish loft’s EPEX membrane sail, whose blend of polyester fibre, film and taffeta can also be fully sourced
from recycled sources.
But Elvstrøm also has a wider approach to sustainability.
All the energy used to make its ‘Ekko’ sails has been sourced from wind generators, while heating in the loft and offices is from woodchip boilers.
The loft offsets emissions from those Elvstrøm suppliers outside Denmark by buying a corresponding amount of extra wind energy under the country’s MedWind programme.
Tackling plastic
Doyle, like Elvstrøm, is looking to reduce plastic packaging waste, as well as sail cloth off-cuts.
This all sounds sensible, but it is eye-opening to hear that off-cuts have been reduced to 5 per cent of Doyle’s sail cloth usage – after efficiency measures were introduced.
Assuming that many lofts will not be so well set up, that raises the prospect that thousands of square metres per day of sailcloth still end up
on cutting room floors.
Doyle’s solution is to use these odds and ends to make beach and sport bags via its partnership with SailGP, as well as to bag up new sails.
It is also looking at sourcing cloths made from recycled materials, but says there will be no news on this until 2024.
North’s mid-range laminate sails are also seeing incremental sustainability improvements.
The transparent film that helps protect the sail from UV is now sourced almost entirely from recycled polyester.
‘We’re paying more for our film today,’ admits Davis. ‘But we’re happy to do it, because it’s worthwhile.’
Eco Sails: High-end problems
In the performance world, moulded or membrane sails sit at the very apex of technology.
Each sail is manufactured to order by a continuous fibre-laying machine, which means there is no waste material. But the emphasis on high tenacity and high modulus means that carbon fibre, aramid and other exotic yarns are often used.
They are much more carbon intensive to produce, require incredibly specialist sailmaking techniques and are even harder to take apart at the end of their lives.
There is research currently ongoing into every aspect of this, but the findings so far are well short of what is needed to create a closed loop for manufacturing.
Pyrolysis of waste carbon fibre creates a ball rather than a continuous thread, reducing its all-important mechanical properties.
And that raises a key paradox. Sails engineered using virgin materials have been carefully honed for the optimum balance of performance and longevity.
Would sailors accept a product that wasn’t quite so good, but came from a more sustainable source?
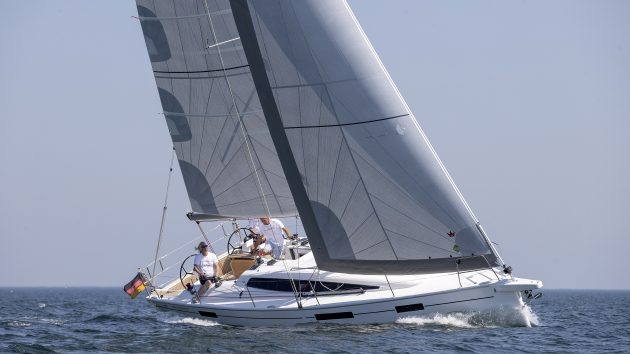
Elvstrom’s Ekko cruising laminate also are fully recycled material. Credit: Andreas Lindlahr
‘Maybe we’ll find out that there’s a willingness to compromise on sail quality to achieve environmental benefits,’ says Davis at North Sails. ‘But if a sustainable sail doesn’t last as long, is it a good solution?’
Many sailmakers think not, and they’ll tell you the best way to reduce the carbon footprint of a sail is to make it last longer.
This is the notion that a quality product may cost more in the short term, but should outperform in the long term.
That means selecting the right cloth for the job, and not being tempted simply to plump for the lowest price on offer, as if all cloth of a certain weight were identical.
‘In particular, it’s the materials – there are cloths that are not up to it,’ says Kay of One Sails. ‘You would hope that any craftsman sailmaker can do the nuts and bolts of engineering the sail.’
Eco sails: Sailors’ choice
Wide manufacturing tolerances in the production of sail cloth means that key characteristics like stretch can vary even within a single roll of material.
‘So, what we’ve always done is to buy woven cloth in rolls of around 10,000m, and each batch is tested at seven points through the roll to create a graph of stretch against load.’
Artificial fatigue is induced by spinning to give a picture of how the cloth will behave.
Sometimes a cloth that was good last time isn’t up to the job next time.
Or perhaps it is too stretchy for a high aspect rig, but fine for use elsewhere.
‘It comes down to the tricks of the trade – elements of the details of the design where you can use other materials to increase longevity.’
In the end, it is developments in other sectors – particularly automotive – that will drive sustainability into sailmaking.
The ability to recycle fibres, and source continuous yarns made from recyclate, will revolutionise the carbon footprint of a sail.
In the meantime, we can order woven polyester sails that are better built and last longer, or alternatively a limited range of laminate sails that offer some green features.
Beyond that, it is simple: maintain the sails well to maximise their lifespan.
A Local Solution
South-Coast sail loft Crusader is working hard to reduce its own impact on the environment.
Waste is minimised by optimising use of sail cloth and canvas, and local partnerships have been established to find uses for old sails, including garment manufacturers and local schools for projects.
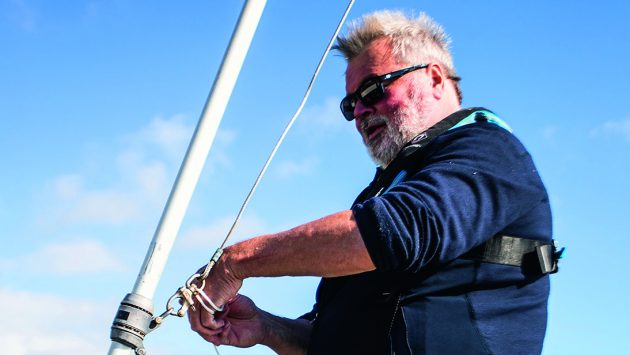
Crusader’s Paul Lees says the loft already has recycling partnerships in place for old sails. Credit: Richard Langdon
Having sails made by your local manufacturer helps to reduce your new suit’s product air miles, compared to sails made overseas, as the cloth may be manufactured in Europe, shipped to overseas factories and then shipped back to the UK, where a loft that can design, cut, sew and service your sails in one place reduces the transport impact dramatically.
The loft now also offers climate neutral sailcloth. Dyneema and other high modulus polyethylene (HMPE) fibres have a large carbon footprint, being derived entirely from fossil fuels.
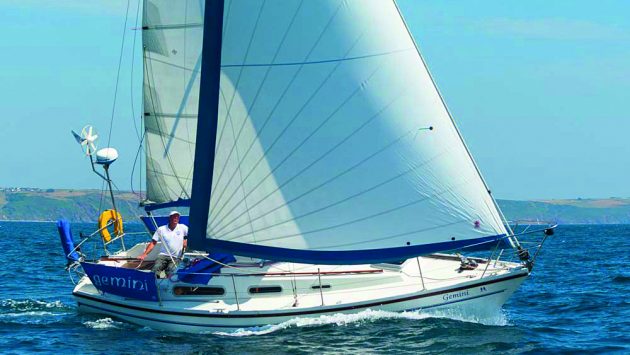
Eco sails: Radial-cut cruising sails by Crusader, which now offers carbon-neutral sails. Credit: David Harding
Bio-based Dyneema uses organic feedstock (timber & pulp) to produce a fibre with exactly the same properties as normal Dyneema but with a fraction of the footprint.
Sailcloth manufacturers Dimension Polyant then weave this into their popular Hydra Net cloth, and reduce the process’s impact by using renewable electricity and offsetting any remaining emissions.
It will carry Dimension Polyant’s cleenTEC seal, and more cleenTEC products are planned.
Cost & demand
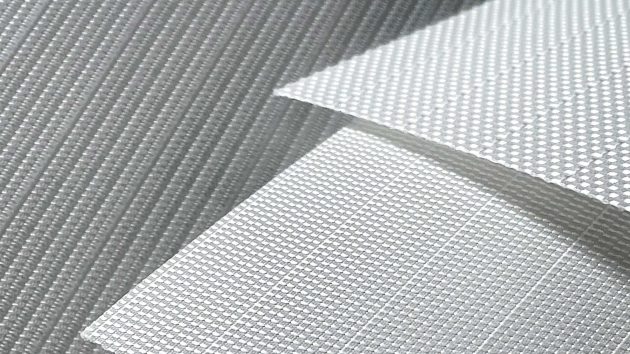
Eco sails: Dimension Polyant are developing a range of cloths made with bio-base feed stock. Credit: Christian Beek
Crusader Sails uses Dimension Polyant’s cleenTEC Hydranet cloth in its premium cruising sails, amongst others.
While the new product is more expensive, Crusader is hopeful that demand is high enough from customers to help drive costs down.
How you know it’s time for a new sail
It can be tricky to spot when your woven sails are ceasing to pull their weight.
Chris Jeckell of the eponymous Norfolk sail loft has this advice: ‘Generally a sail needs replacing once the sail has become baggy or misshaped as the performance will suffer and this means that the draught in the sail has moved aft making the sail much deeper and harder to trim.
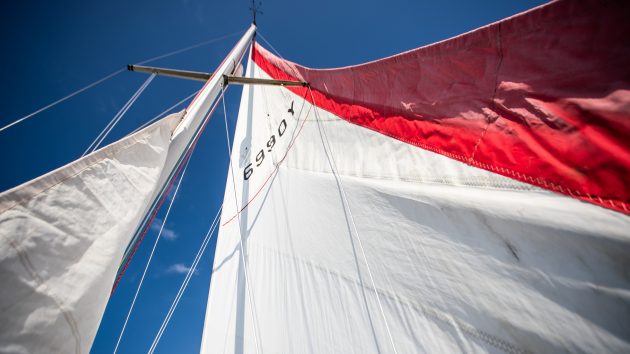
Look at your sails both under load and not under load to look for wear, stretch and draught. Credit: Richard Langdon
‘A good way of checking the draught is to take a photo up the sail from the mast. Draw a straight line between the luff and the leech. If you do this each year you will be able to watch the draft move aft. Also, if you need a lot of helm to go in a straight line, this is a good indication that your sails are baggy. UV damage is another sign to look for as the cloth breaks down and becomes weak and will cause the sail to rip.’
Laminates sometimes fail more dramatically, but the more usual warning sign is parts of the laminate wearing through in high-wear areas.
Once you see mildew inside the laminate, you know the structure has been compromised and then it is usually just a matter of time.
Enjoyed reading Eco sails: options for sustainable sails?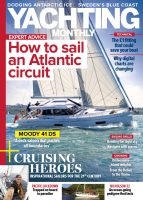
A subscription to Yachting Monthly magazine costs around 40% less than the cover price.
Print and digital editions are available through Magazines Direct – where you can also find the latest deals.
YM is packed with information to help you get the most from your time on the water.
-
-
- Take your seamanship to the next level with tips, advice and skills from our experts
- Impartial in-depth reviews of the latest yachts and equipment
- Cruising guides to help you reach those dream destinations
-
Follow us on Facebook, Twitter and Instagram.