Regular checks can help prevent catastrophic ballast failure, which can be seriously dangerous and occasionally fatal. Ben Sutcliffe-Davies explains what to look for…
Few yachts have issues caused directly by the design of the keel. Almost all the failures I deal with are from hull damage that has gone unnoticed or poor repairs of common problems, such as constant, regular grounding, or rare incidents such as contact with a submerged shipping container.
While it’s important to check keel fittings over time for signs of stress, the most obvious moment to check them is following a grounding. Groundings come in two forms: the regular expected grounding and refloating of a boat left on a drying mooring, and sudden, unexpected groundings. It’s important to remember that sand can be surprisingly hard to ground on, while mud can create suction tight enough to hold the hull, and even force the hull and keel fastenings apart.
If you accidentally find the seabed, there are several actions you should take as soon as possible to check whether there has been any significant damage. It goes without saying that you should have your boat lifted and inspected after any significant unexpected grounding.
With bilge-keelers, even if there is no damage internally, repeated intentional groundings can eventually cause the keels to splay apart, bending the studs and weakening the laminate. This should be checked on an annual basis, ideally at lift-out for winter.
In the 1970s and 1980s many boat builders, such as Moody, used iron studs and coated the fastenings and backing plates with gelcoat. This never caused much of an issue other than some corrosion to the nuts and backing plates that frequently develop when they are exposed to wet bilges over a long period of time, or with some movement or stretching of the fastenings where they needed torquing down.
On the majority of modern production yachts these days, the keels are secured with stainless steel studs or bolts that are wound down into the casting. These, just like iron fittings, are perfectly acceptable as long as moisture can be reliably prevented from reaching the fastenings.
Sealant failure, or fastenings not being torqued regularly (every seven to ten years), can lead to moisture ingress into the hull-to-keel joint, causing crevice corrosion to stainless steel when oxygen cannot be replenished due to the fact that the chromium layer stops reforming. Over the years I’ve seen some spectacular failures in stainless-steel fastenings when used under water.
So, when it comes to looking after your keels, try to keep your bilges dry and your fastenings clean internally, inspect them regularly, and don’t ignore the sealant around the hull-to-keel joint. And do try your best to keep away from sandbanks!
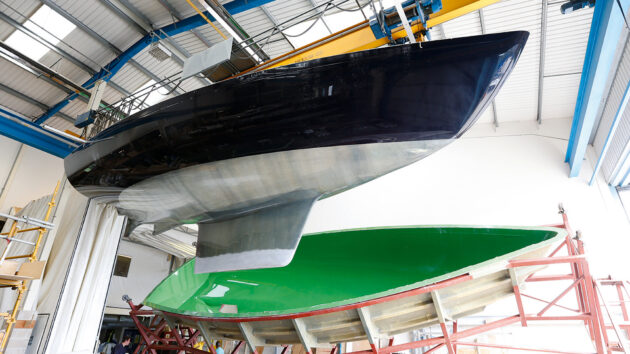
Freshly released hull moulding, showing the encapsulated keel of a Rustler 37. Photo: Graham Snook
Encapsulated keels
Many boats built in the 1970s and 1980s have encapsulated keels, where the keel is moulded as part of the hull, then filled with ballast. The ballast can range from lead ingots to steel punchings (the middles of washers). The way the metal is embedded into the keel void can range from having a mixture of sand and cement to, if you’re lucky, steel punchings mixed into polyester resin.
An encapsulated hull is considered to be the strongest and safest way of incorporating a keel. However, sailing performance, compared to a modern keel profile, will be significantly reduced with the production process also relatively more costly and time consuming. Another disadvantage is that if the keel gets damaged water can work its way into the ballast chamber and, if iron-ballasted, will cause corrosion and material expansion issues.
If you have encapsulated ballast, check it regularly by lightly tap-testing and listening for detachment of the ballast, looking carefully for swelling or splits around the keel lamination. Pay close attention to the leading edge and underside of the keel where it may have hit obstructions or been abraded. Water causes iron ballast to swell as it rusts which can lead to bulges in the hull. Lead won’t rust or swell, but trapped water will swell if it freezes.
External keels
The most common material used today to bolt on external keels is stainless steel. We no longer see many builders using high tensile steel or silicon bronze (a low-lead brass alloy). The sizing of the backing plates used to secure an external keel is vital. I’ve seen some backing plates buckle under normal use where the size and gauge of the plates haven’t been big enough.
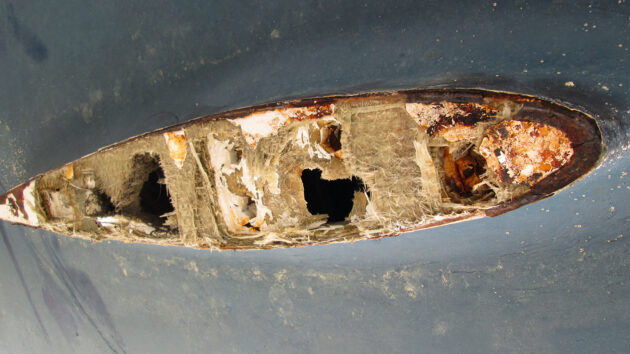
Yachts can sink if high moisture content compromises the strength of the laminate. Photo: Ben Sutcliffe-Davies
Combination keels
Some builders use a combination of a lead bulb and a cast iron top section, which is generally considered to be a good compromise, but it can lead to issues with how the two materials are connected. Some builders use long bolts that run through the iron and then secure within, or even pass right through, the lead base.
Know your keel fastenings
Get to know where the keel fastenings are on your yacht. They usually align with the main areas of the keel, but there will sometimes be a smaller fastening forward and aft. Look for any evidence of weeping around the fastenings or under the plate washers.
If you have clean bilges and there are areas of staining developing from under the fastening washers, there may be an issue. Using a camera to take photos and then magnifying the images is a useful way to identify problems up close and in detail. Lightly tapping the tops of the fastenings with a small hammer will also help identify issues, with dull notes indicating that a particular fastening is no longer under the same tension as the others. Be mindful of when they may need to be torqued up.
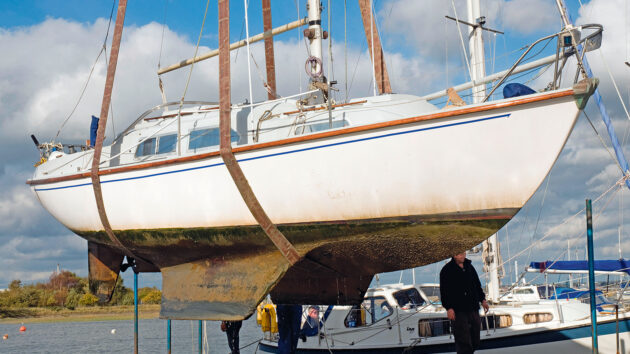
The best time to test keel safety is when your boat is held up on strops. Photo: Tim Woodcock / Alamy
Inspecting keel bolts
A visual inspection is advisable every season. Make sure the bilges are dry, then look for moisture seepage around the fastenings. Use a small hammer to tap-test the fastenings, and inspect the laminate around the fastenings for potential stress. If possible, inspect the craft when it’s lifted out the water and on strops, looking for any gapping of the keel joint.
If you are able, do a tip test of the keel with some light sideways force, and check for movement or deflection of the hull around the root. When the yacht is set down, look for movement between the keel and hull or sagging along the keel. Any movement or opening of the joint needs a further proper inspection by a professional.
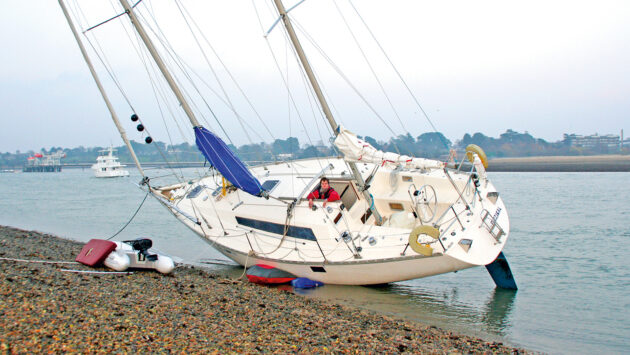
Always check your keel after any unexpected grounding. Photo: Kieran Flatt
Checking a bolted-on keel
Bolts holding on an external keel will have been specified by the designer to have an infinite fatigue life, so loads applied to them in normal use should never be high enough for fatigue to be
an issue. Fatigue should only arise where corrosion has removed load-bearing areas from the bolts. Small failures can allow the keel to move, spreading to separation of structures, loss of strength, and, ultimately, the loss of a keel.
Several signs might indicate that all is not be well with your keel and its supporting structures. The checks that follow (see right) should be undertaken after any unexpected grounding, or if you have never done them before.
If you are in any doubt, seek advice from a surveyor or experienced repair yard. If you’ve had an incident, contact your insurance company as it may want to appoint a surveyor of its choice.
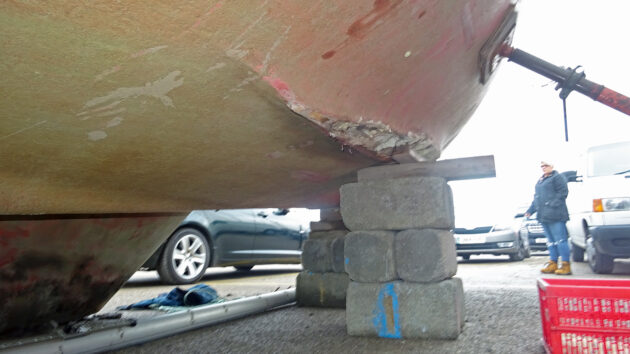
Regular external checks can prevent catastrophic keel damage. Photo: Ben Sutcliffe-Davis
External checks
When the boat is lifted, look at the hull-to-keel joint to see if there is a gap between the keel and the hull. Does the gap close when the boat is put down? A hairline crack in the antifouling is normal at a hull-to-keel joint, especially if flexible sealant has been used to seal the joint.
Are there streaks of corrosion from the hull-to-keel joint? It can be hard to judge the origins on an iron keel. Corrosion on the top flange of the keel can start loading stresses. Corrosion streaks developing on
a lead keel with stainless steel bolts must be taken seriously.
When the hull has dried out, is there water still leaking from the hull-to-keel joint? This is a clear sign that the seal has failed.
Can you see cracks or damage on the hull? The keel may have moved and dislodged some paint. You may have to remove the coatings to expose the hull, but in some cases the cracks are clearly visible.
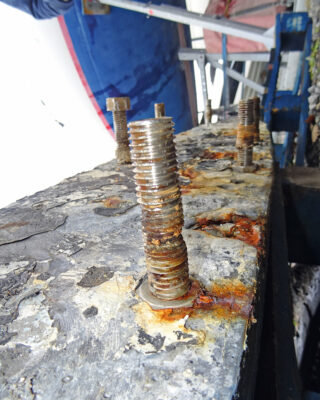
This stud with crevice corrosion wouldn’t have been discovered if the keel hadn’t been removed. Photo: Ben Sutcliffe-Davis
Another obvious test is to push the bottom of the keel to see if you can move it. Does it swing when you let it go?
With the boat resting on the keel, can you see any upward deflection of the hull? This can sometimes be seen aft of the keel where the hull should be flat and is less likely if there is a keel stub. Failure in any of these tests suggests the keel structure may have been weakened, and further investigation is required.
Internal checks
Is there water in the bilge? Leaking keel bolts are a sure sign all is not well, particularly with stainless steel. Check for other more obvious leaks, including the plumbing, to eliminate them before tackling the bolts.
Look closely at the keel bolts, nuts and washers. Use a brass wire brush to remove built-up crusting and debris. Steel bolts often look terrible at first, but further investigation might reveal no significant loss of material.
Nuts can be removed one by one to allow inspection of the threads below. New nuts may be needed if there is any damage to the old ones.
Tea staining around stainless bolts should be taken seriously. If you believe your stainless steel keel bolts have been wet for some time, you must suspect they are corroding and take action to investigate.
Is there any sign the bolts have moved? Check for tell-tale marks on the hull which may indicate this.
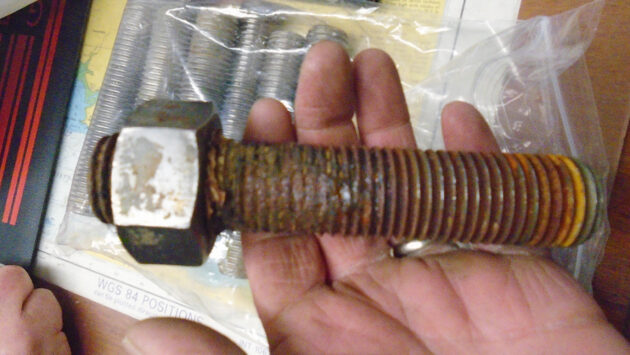
Example of a worryingly corroded keel stud. Photo: Ben Sutcliffe Davies
Are the nuts tight and washers still flat? Enlarged holes and re-tightening of nuts can deflect washers into a cup shape. Glassed- over studs may have corrosion stains visible, and a light hammer may reveal one that sounds different from the rest.
Do the sole boards fit and are the sealant bead joints still in place around the bulkheads? Do the doors still open and close? All can indicate the hull shape has changed. Look closely around structures that support the keel. You may have to remove screwed-down sole boards.
Laminate fractures are a clear sign of movement beyond design, and a gentle hammer tap-test can be used to find areas where the internal pan liner and matrix structures have detached from the hull.
Are there signs of repair? Is there a record of the repair? Poor finish and different colours are easy to see (as is dust) in hard-to-reach spaces. Signs that the keel was not removed, such as resin over the keel bolts or repair edges around the keel bolts, might be signs of inadequate ‘sticking plaster’ repairs. Painted studs and nuts may be a sign of good maintenance but could also be an attempt to hide something.
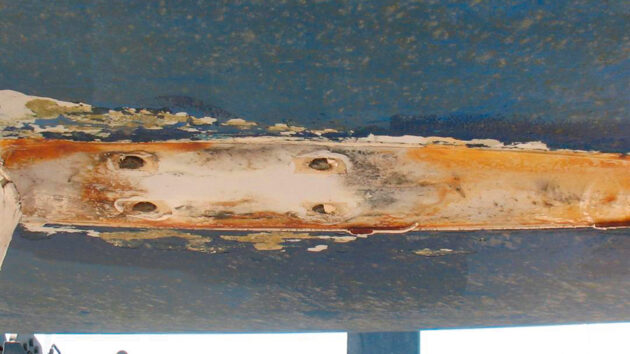
Damaged keels often have to be chiselled away from the hull. Photo: Ben Sutcliffe-Davis
Removal of the keel
If you suspect that your keel bolts are failing or might have an issue, the only way to be sure is to remove the keel to have a look. This shouldn’t be taken lightly and will probably require mast removal in the first instance and a hoist or crane to support the boat. Have a strong structure ready to support the keel. Damaged keels might not lower easily and may have to be chiselled off.
If you find or suspect damage to the internal structure, then a full repair is likely to require the keel to be removed to allow the hull to regain its proper shape. A few bits of matting and resin are seldom enough to replace lost strength. If you are in any doubt you should seek advice from a surveyor or yard with experience of keel repairs.
If you suspect you have a problem, contact your insurance company as you may be able to recover some of the cost.
Enjoyed reading this?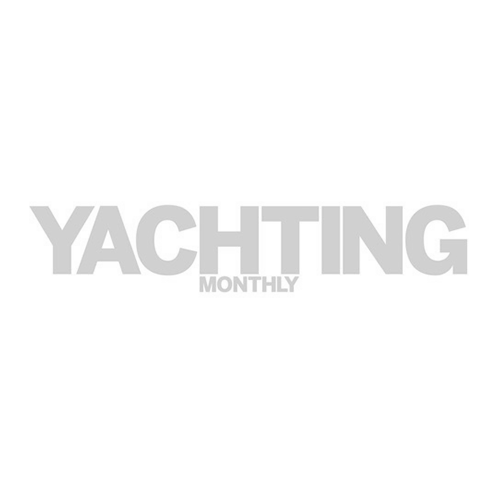
A subscription to Yachting Monthly magazine costs around 40% less than the cover price, so you can save money compared to buying single issues.
Print and digital editions are available through Magazines Direct – where you can also find the latest deals.
YM is packed with information to help you get the most from your time on the water.
-
-
- Take your seamanship to the next level with tips, advice and skills from our experts
- Impartial in-depth reviews of the latest yachts and equipment
- Cruising guides to help you reach those dream destinations
-
Follow us on Facebook, Twitter and Instagram.