Eventually all batteries reach the end of their life, but is lithium the green solution it is held up to be and what technology is being used for recycling bateries? Sam Fortescue investigates
Batteries are in many ways anathema to sailors. They are heavy, finicky things, whose performance wanes with time, requiring an elaborate system to keep them in good shape.
They are also, when you get down to the level of individual cells, thoroughly analogue – even if a host of clever digital battery management systems have grown up around them.
As consumables, they need regular replacement – perhaps as often as every five years, depending on how kind you are to them and how much they are used. So in one sense, at least, sailing is the process of turning a steady flow of new batteries into waste, which, like all waste, has to be dealt with.
It is something of a dark art to know when your lead-acid batteries need replacing. But the most basic way is to measure the voltage after a full charge and a period of settling. A voltage below 12V indicates total failure, while 12.20V-12.35V indicates around 50% state of charge (it varies slightly according to whether your battery is wet-cell, gel or AGM).
A healthy battery should measure 12.70-12.85V. You could also measure the specific gravity of the electrolyte after a full charge, which equally tells you how much capacity remains.
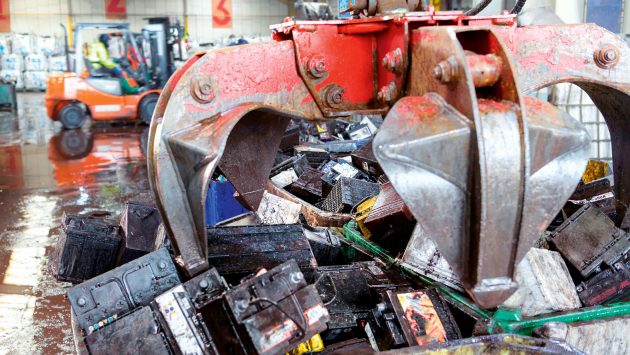
Almost all the materials in lead acid batteries can be recycled. Photo: Cultura Creative Ltd / Alamy Stock Photo
How much capacity is enough? Well, that is up to you. But if the lights flicker when the water pump starts up or you find yourself running the engine more and more regularly to keep the fridge running, there could be a problem.
Be particularly alert to changes that might hint at a decline in performance. When you’ve had enough, it’s time to replace the whole battery bank.
Old tech benefits
Fortunately, the most common sort of lead-acid battery is almost completely recyclable. Better still, it is the manufacturer or retailer’s legal duty to collect the batteries and pay for their processing. Retailers are obliged to accept your old battery back in return. You can also drop them at the local dump.
‘If you take an individual lead-acid battery, about 99% of the battery can be recycled,’ explains Tom Spinks of Enersys, which manufactures about a million lead-acid batteries each year at a plant in Newport, Wales. ‘There are just small residues, like glues or resins, that can’t be recovered. The lead, the plastic, even the glass matts can be reclaimed.’
Whatever flavour of lead-acid marine battery you use, it is a big heavy-duty plastic case filled with lead plates and either a liquid or a gel-based electrolyte.
As much as 60-70% of the weight of these batteries is accounted for by the lead alone, and there is both a legal and an economic motive to reclaiming it. Of the balance, sulphuric acid forms roughly half, followed by the polypropylene of the battery case, then other plastics and other additives such as glass and carbon.
Recycling these batteries is a relatively primitive process. ‘The recycler smashes it up using a set of choppers to break the battery down,’ explains Spinks simply. ‘The mix of liquid and fragments then goes into a gravity separator, which allows the heavy metals to be collected separately from the floating plastic shreds.’
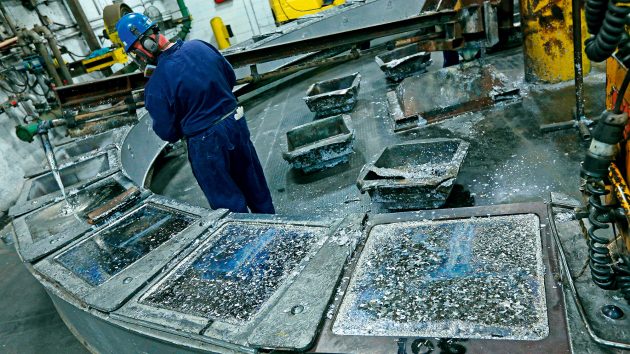
Lead is easily smelted
down and recast. Photo: Tribune Content Agency LLC / Alamy Stock Photo
Worth over $2,000 per tonne, lead is the most valuable material from this mix, and it can be re-smelted into pure metal that is eminently suitable for fashioning into new batteries.
In this way, a significant portion of modern battery production takes place on a closed-loop basis. The same goes for the plastic of the casing and even the acid, which needs just to be reconcentrated.
Across the world, it is reckoned that some 98% of battery lead is successfully recycled – a relief when you consider the environmental harm it could do. The industry is quick to describe this as ‘the environmental success story of our time’.
Some brands say that their specific battery chemistry supports this process. For example, Enersys brands use a proprietary construction called ‘thin-plate pure lead’ (TPPL), which means that the metal is of a particularly high purity and consequently easier to extract for re-use.
‘The purity of the materials gives you that additional reliability and endurance, as well as higher peak currents, lower voltage drops, and faster recharge times,’ says Spinks. ‘One of the things that hasn’t been recognised is the differentiation of TPPL batteries. That’s why we have developed the AGM2 standard.’
Carbon is another additive that has proven valuable in other battery types. By including some carbon in the negative plate, battery life can be increased by
50%, Enersys says, with a more robust response to the partial recharging that commonly accompanies off-grid renewables, such as solar or wind.
Other brands such as Victron and Trojan also include use carbon.
Young upstart
Lead-acid batteries may be the backbone of the marine accumulator market, but the upstart lithium-ion batteries are making inroads. And that is a completely different story.
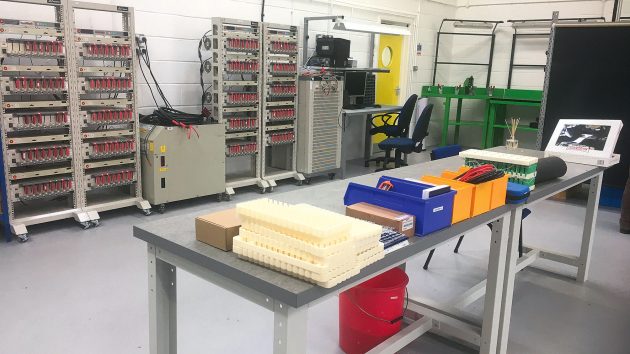
Aceleron makes modular lithium batteries
In 2010, Friends of the Earth estimated that a pitiful 5% of lithium-ion batteries were recycled worldwide, most ending up in landfill. A more recent estimate from London’s Circular Energy Storage puts lithium recycling at closer to 50%, or some 210,000 tonnes of batteries last year.
The vast majority of this activity is based in Asia, so whatever the true figure, Europe is racing to catch up.
There have been small lithium batteries on boats for decades, via handheld navigation devices and other portable electronics. More recently, lithium has found a niche as a house battery for high-performance sailors. But as in the automotive sector, it is mainly the advent of electric propulsion and electric yachts that is bringing lithium flooding aboard.
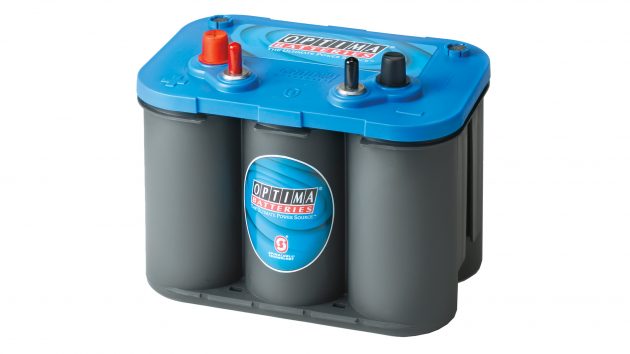
Optima uses spiral cells rather than flat plates
Lithium has much greater energy density than lead, as well as better charging characteristics. And you can repeatedly discharge it beyond 80% of its capacity without damage, whereas a lead-acid battery only supports 40-50%.
It all adds up to a service life of up to 3,000 cycles for lithium – equivalent to about 10 years’ continuous use. But in the end, they do also deteriorate.
Lithium ions are lost as a deposit, and the pores in the separator between the cathode and the anode can become clogged and useless. Just like sulphation in a lead-acid battery, lithium-ion batteries will lose capacity over time.
Types of lithium batteries
- Lithium iron phosphate (LiFePO4 or LFP): Most common variety used on boats. Durable, safe and deep-cycling but less energy dense than other types.
- Lithium cobalt oxide (LCO): Often found in cameras and phones, where constant low power and high energy density are ideal. Costly.
- Lithium manganese oxide (LMO): Used in power tools and some EVs. High power and fast charging but shorter lifespan.
End-of-life quandary
‘There is not a clear standard to define the end of life for a lithium-ion battery,’ says Steve Bruce, UK distributor for ePropulsion electric outboards and drives. ‘Normally, a power battery would reach the end of its life when it retains 70-80% of its original storage capacity, and the main reason for decommissioning is that it is inefficient for propulsion.’
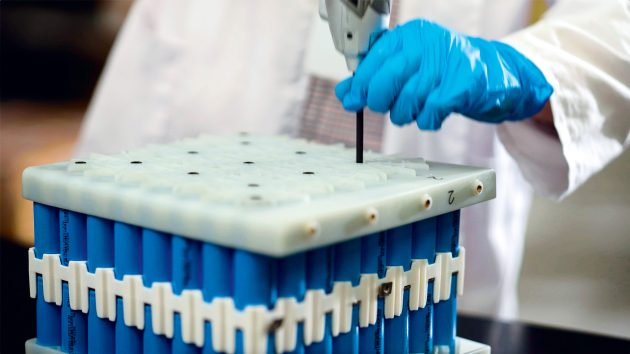
Aceleron’s modular batteries allow you
to replace individual cells that fail, dramatically increasing the life of the battery
Electric propulsion is a relatively new technology in the marine sector, so few lithium batteries on boats have reached this point yet. In around a decade’s time, when that begins to happen, there are a number of options.
At the top of the list is so-called ‘repurposing’, where the battery is moved to a function that is less dependent on outright efficiency.
‘With regard to ePropulsion, it recommends that its batteries are repurposed at the point they become less effective for propulsion,’ says Bruce. ‘Examples include for the storage of energy from home solar, heat pumps and so on. That way, their life can be extended for years.’
In this case, larger batteries are stripped back to their individual modules and cells, which are tested and evaluated. Europe is playing catch-up on this, but companies such as Cellcycle in Manchester and Ecar in the Netherlands are part of a growing infrastructure of small businesses. Good cells are sent on to specialists who can recombine them into new batteries; fuses, chips and other hardware are sorted and reused or recycled.
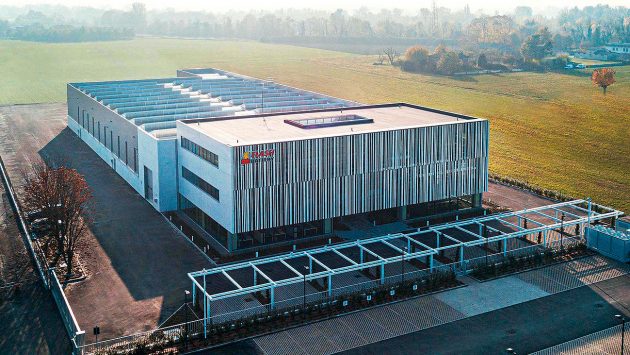
Flash Battery is trying to develop a solid-state lithium battery
British start-up Aceleron is making a virtue of this process by building the first ever fully modular lithium battery. Its 1200Wh Essential battery is designed for easy disassembly so that dead cells can be identified and replaced.
In this way, the battery can be renewed three or four times for a lifespan that eclipses that of cheap mass-produced batteries. ‘You should never need to throw our battery away,’ says COO Bruce Macdonald. ‘It’s all about that capability to service them and extend life. We’re preventing a lot of material going
into the back-end recycling chain.’
Old cells don’t just end up going into home solar or wind set-ups, either. Repurposed lithium-ion batteries could be used as house batteries on boats, where they preserve an advantage over lead-acid batteries but for a much lower price than virgin lithium. Dutch Craft uses reconditioned Tesla batteries, for example.
And Aceleron markets a much cheaper green-box battery that has 20% less nominal capacity than a new one at just 35% of the price.
Hard to recycle
When a lithium battery really has reached the end of its life, and is failing to perform, then it can still be recycled, although many clearly are not. And it is here that lithium’s chief disadvantage makes itself felt.
It is a very reactive element – as you might remember from those science experiments in the fume cabinet at the back of the classroom. Combine lithium with water and the result is literally explosive.
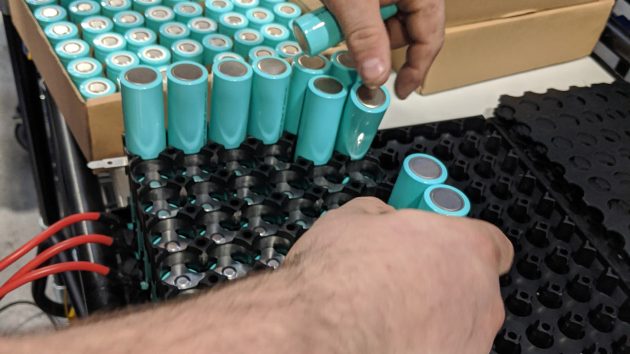
Individual Li-Ion battery cells
Fortunately, there are signs that the waste management industry is investing in processes to safely recover metals from old lithium batteries. RS Bruce has just commissioned the UK’s first such plant in Sheffield, which can handle around 1,000 tonnes of lithium batteries per year.
It claims a recovery rate of more than 80% using a low-energy process that doesn’t rely on cooking the battery waste like some others.
‘Within the cell itself, you’ve got three layers: aluminium coated with cathode powder – a compound containing an oxide of lithium and other metals including cobalt and nickel; a plastic separator soaked in electrolyte; then copper foil coated with graphite,’ says Sam Haig of RS Bruce. ‘It’s sandwiched together inside the cell. The recycling process shreds that open to expose the materials and separate them.’
The lithium itself is not the target of this process. Instead, the most valuable output is a ‘black mass’ containing copper, aluminium, nickel and cobalt. One of the problems is that the headline lithium has until recently retained a fairly low value on the London Metal Exchange.
A year ago, lithium bottomed out well below $8,000 per tonne, whereas cobalt is trending up at some $73,000/t and nickel at more than $20,000/t. For us as end-users, it makes little difference. The legal onus is on the people who sell us batteries to collect them and pay for their recycling, without charging us directly.
The only problem is that recycling is a net cost to the industry – even with sky high metal prices. ‘When you talk about the economics of recycling, pretty much all batteries have a cost for recycling,’ says Haig. ‘The material value doesn’t pay for the cost of recycling – those disposing of the batteries are paying for it.’
And that situation is only going to get worse as battery makers develop cheaper chemistries that can be more efficiently mass-produced. Valuable cobalt is already in the firing line, with the US aiming to eliminate it from batteries by 2030 to sidestep China’s stranglehold on global supply.
‘If the market shifts towards battery technologies such as LMO and LFP, then the cost of recycling is going to have to go up, because the value of the materials you recover from them cover less and less of the cost of the recycling,’ adds Haig.
As it did with lead-acid battery waste, regulation is going to poke its nose into lithium and force change. At the moment, lithium-ion batteries are not even named in the legislation, and those who sell them can service their recycling obligation using easier lead-acid batteries.
UK and EU regulators are floating new rules that would see at least half of lithium batteries collected, and even force manufacturers to use recyclate in their new batteries.
That’s something that doesn’t seem to worry Britishvolt, the government-backed start-up building a vast new lithium-ion battery factory on the Northumberland coast at Blyth. It has signed a deal with Glencore to recycle 10,000 tonnes of lithium batteries per year by 2023.
Perhaps this is the scale required to ensure lithium batteries join the circular economy at last. ‘This exciting project adds much to our existing relationship with Glencore supplying Britishvolt with responsibly sourced cobalt,’ says Tim Orlob, COO of Britishvolt. ‘Recycling is key to a successful energy transition.’
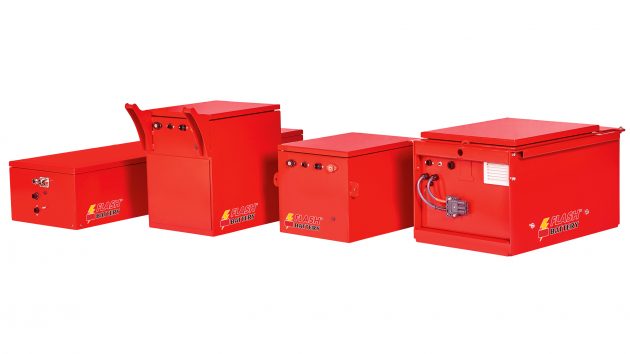
Flash Battery makes lithium batteries for industrial and transport applications
Battery of the future
Lead-acid battery makers are busy trying to differentiate their products with jazzy descriptions like ‘high-density active paste’ or ‘Maxguard separators’. Thinner, purer lead plates have certainly improved performance, as has including carbon.
But for the next generation, you have to look at more ambitious design changes. ‘The next thing may be bi-polar batteries, where the cathode and anode are mounted on the same plate with a hard wall between them,’ says Tom Spinks of Enersys. ‘We’re a few years out, but it would offer higher power density – more power in the same space.’
On the lithium side, the hope is to develop solid-state batteries where the electrolyte is a metal. Proven in the lab, these are more energy dense and much faster to charge than current liquid electrolyte batteries.
‘I certainly see plenty of opportunities for solid-state technology,’ says Flash Battery founder Marco Righi. ‘It is now at a development stage and the first actual production is expected in 2024.’
Other avenues include:
- Sodium-ion batteries with a fraction of the cost and environmental damage associated with lithium.
- Aluminium-air batteries – many times more powerful than lithium-ion units, with a rechargeable chemistry.
- Nano structures can enable existing battery chemistries to produce more power and recharge more quickly.
Enjoyed reading this?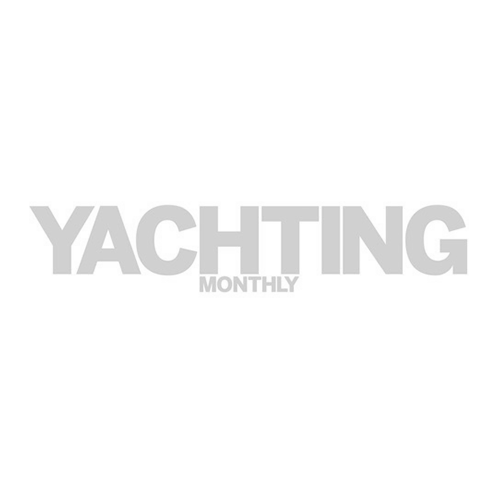
A subscription to Yachting Monthly magazine costs around 40% less than the cover price.
Print and digital editions are available through Magazines Direct – where you can also find the latest deals.
YM is packed with information to help you get the most from your time on the water.
-
-
- Take your seamanship to the next level with tips, advice and skills from our experts
- Impartial in-depth reviews of the latest yachts and equipment
- Cruising guides to help you reach those dream destinations
-
Follow us on Facebook, Twitter and Instagram.