The marine industry is puzzling over how to dispose safely of redundant, environmentally toxic GRP-built craft. Ollie Taylor investigates
The annual volume of composite waste generated by the marine industry each year is a staggering 55,000 tonnes – and it’s predicted to increase by 10% every year in the near future as more and more leisure yachts reach their end of life (EOL).
Glass reinforced plastic (GRP), commonly known as fibreglass, is the wonder material that created the modern leisure marine industry back in the 1960s, transforming what was once an artisanal, predominantly wood-based industry, into the high volume mass production model now pumping out an estimated 10,000 new boats in the UK alone each year.
However, GRP, and the successful lightweight, rigid structures it produces were never designed with an EOL solution in mind, leaving today’s boatbuilding industry scratching its head for a solution to what is becoming an increasingly urgent problem.
There are an estimated six million boats in the EU at the moment, 95% of which are made of GRP. Each year, 1-2% (60,000-120,000) reach the end of their usable life.
The fate of these craft is relatively unknown but it’s estimated that only 2,000-3,000 are properly recycled each year. And, unfortunately, there are several fundamental challenges that currently restrict the marine industry and its ability to solve this problem.
Composite structures, such as GRP, by their very nature are designed to last a long time, delivering very specific material properties. Stronger than many metals by weight, non-conductive, and with the ability to be moulded into highly complex shapes, GRP is the perfect material for making boats in high volumes and at low cost. However, the process of combining glass fibre with a thermoset resin to achieve the properties modern designs need results in a structure that was never meant to ever be separated again.
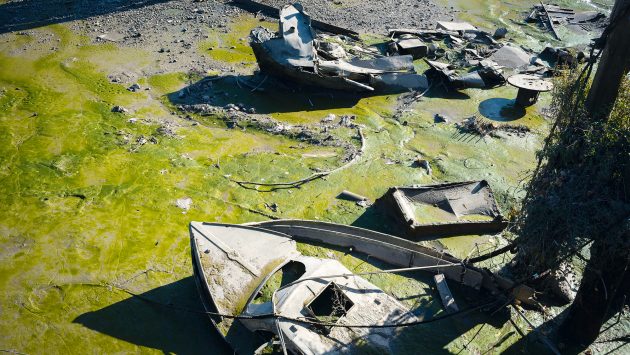
Derelict boats sit in low-tide river mud and silt on the River Thames. Photo: Richard Baker / Boatbreakers.com
So why has this problem not been addressed before now? The average lifespan of mixed composite laminates is anywhere between 25 to 100 years, and most usually towards the latter end of that scale. Given that GRP was widely adopted in the marine industry during the 1960s and 1970s, we are only now reaching the point where a high volume of vessels are beginning to reach the end of their life. This ticking time bomb is combining with a fast-evolving and much stricter waste control landscape than seen in previous decades.
A number of European countries have banned, or soon will ban, fibreglass waste from landfill completely, so finding a secondary purpose for waste GRP will be critical.
By reducing our demand for virgin raw materials, and thereby reducing our negative impact on the environment, we can begin to solve this urgent and growing problem for the maritime industry.
Recycling technologies
Five main recycling technologies offer potential solutions to how we can deal with the 55 kilotons of GRP waste the industry creates each year: mechanical grinding; incineration with energy recovery; co-processing in cement production; pyrolysis; and solvolysis.
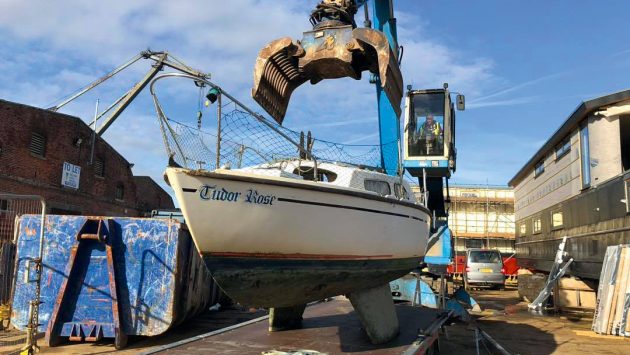
Crushing old boats yields low recycling and economic returns. Photo: Richard Baker / Boatbreakers.com
Mechanical grinding is the most widely available recycling process, although still only at a small scale compared to other processes such as glass recycling. It takes small to medium-size GRP panels through multiple stages of crushing and grinding to reduce the material into small fragments or powder. It doesn’t separate the fibre from the resin, or any other laminate reinforcements (plywood or foam core, for instance).
Instead, it lumps everything together, resulting in a material that has limited mechanical properties and thus very low financial value. The recyclate can be used as a filler or bulk agent in new composite products. However, market demand for it is low, while the cost and energy required to complete the process is relatively high.
Incineration with energy recovery converts fibreglass panels into energy by burning the organic resin element to create heat which can be converted to electricity via steam turbines. Unfortunately, the glass fibre element has no calorific value and limits the ability for generating energy. It has also been documented that using domestic refuse incinerators for GRP tends to overload the incinerator and displaces domestic refuse which may end up in landfill rather than being incinerated.
The biggest challenge is the creation of bottom ash from the process which is typically sent to landfill. Very few commercial incinerator operators actively choose to take GRP waste as it’s a tricky material to deal with.
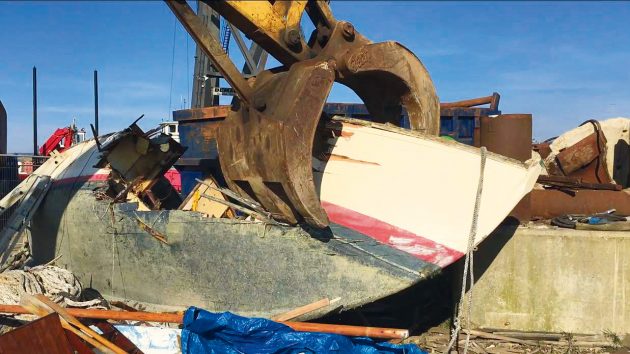
Crushed material often still ends up in landfill. Photo: Richard Baker / Boatbreakers.com
Co-processing in cement production uses almost 100% of the EOL composite. During co-processing the waste is simultaneously used as both an energy source (the resin) and a raw material input (the fibres) into clinker cement production.
There is a growing consensus that this solution could significantly reduce the greenhouse gas emissions of the cement industry whilst also solving the EOL composite waste conundrum. Cement production is one of the world’s biggest causes of carbon pollution, responsible for 7% of global emissions, equivalent to more than any country except China and the US. Unfortunately, this process is still operating at a relatively small scale, but we’re likely to see a widespread scaling up of the technology in the near future. However, it is still considered to be ‘downcycling’ as you are not actually reclaiming the original material inputs.
Pyrolysis and solvolysis both use a combination of high heat (pyrolysis) and chemicals (solvolysis) in the absence of oxygen to break the composite down into its separate fibre and resin components. The incineration temperatures range from 300-700°C and essentially burn the resin from the fibre. It currently only operates at academic or pilot scale. The very high cost of running the process means it’s geared towards carbon fibre reclamation only.
The benefit is that you end up with the raw fibre, which can be reused. The downside is that recycled fibre is short and discontinuous, requiring further processing. Lineat, a new company based in Bristol has come up with an innovative solution for realigning the reclaimed fibres into uni-directional discontinuous fibre tapes that can be used in a wide range of new composite products. The tapes retain >75% of the strength and >85% of the stiffness of continuous virgin carbon fibre tapes.
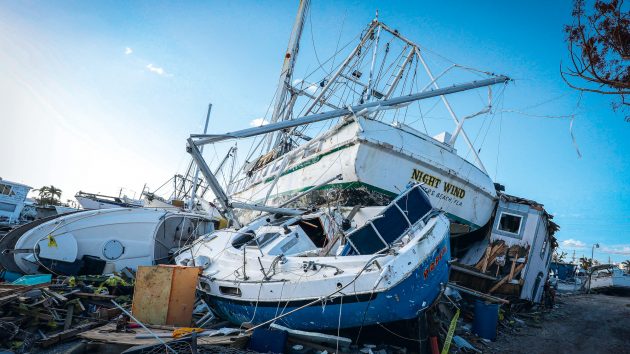
Hurricane Ian in Florida saw hundreds of boats suddenly reach their ‘end of life’. Photo: AFP via Getty / Boatbreakers.com
The process takes the short, reclaimed fibres and immerses them in a liquid which is then fired through a small nozzle to realign all the fibres into a straight line. The newly aligned fibres are then combined with a resin to create a pre-preg tape. Again, this technology is operating at a small scale, but it has proven that we are now able to use reclaimed carbon fibre.
Price incentives
The key barrier to all of these processes reaching widespread scale and adoption is money. The price of virgin raw materials remains incredibly low, and the incentive to use recycled raw materials is almost non-existent as the price and availability of virgin materials is more attractive. This is combined with the fact that most recycled materials often have worse mechanical properties than the virgin material, and in a world of high performance lightweight structures there is little room for performance trade-offs.
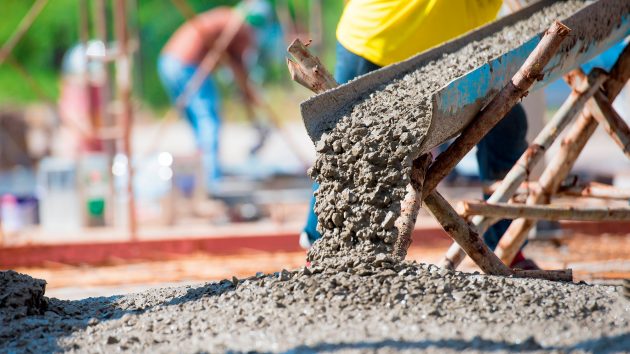
Recycled boat composites used in concrete production could help reduce the construction industry’s environmental impact. Photo: Jung, Getty
Due to the low demand and the commercial value of the recyclate from the processes shown above, few operators are willing to invest in developing suitable infrastructure to perform the process. That leaves the marine industry in the chicken and egg situation of having no suitable infrastructure development and no commercial incentive for investors to fund development.
APER scheme
However, there is some good news. France’s APER scheme offers a glimpse of what is possible when the marine industry works collaboratively.
APER is a world first which requires French manufacturers to pay an ‘eco-contribution’ for every new boat sold. That money is then supplemented by contributions from the national annual taxation on recreational craft, giving the scheme an operating budget to deal with recycling the legacy fleet, partially funded by the new fleet.
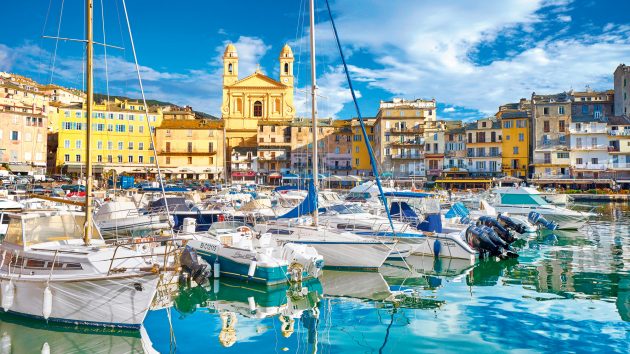
Leading the way: France already has 30 approved boat recycling centres. Photo: Jan Wlodarczyk / Alamy Stock Photo
In 2022, the scheme recycled 2,980 boats and is now building up its infrastructure to deal with around 3,000 vessels per year, ranging from 2.5m to 24m. The scheme currently has 30 approved deconstruction sites across France catering for most regional boating centres. At present, just over 60% of the composite waste is sent for incineration with energy recovery, while the remaining 40% is ‘disposed’ of, although it’s not clear if this simply means landfill.
The other main components are separated and sent to their respective material recycling processes.
Producer Responsibility
The APER scheme is an example of ‘extended producer responsibility’ (EPR), a legislative instrument that will significantly change how new products are designed, used, and treated at EOL in the future. EPR works on the simple premise that the original manufacturer retains responsibility for the item when it reaches its EOL.
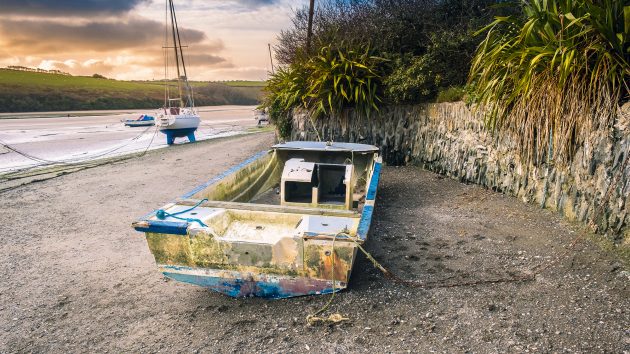
Where abandoned wooden boats would have rotted away, GRP remains in the environment indefinitely. Photo: Gordon Scammell
Legacy fleet
So where does this leave the marine industry? The problem can be split into two distinct categories: the legacy fleet; and the new fleet.
How we reuse, recycle or recover materials from the legacy fleet remains unclear. What is becoming evident, though, is the need to collaborate across various industries to scale the technology and build the required infrastructure. The marine industry will not solve this problem in isolation. Even then, the need to develop innovative and commercially viable uses for the recyclate itself is paramount.
If this can be achieved, the vital investment required to scale the technology will come. Ultimately, the power to completely remove this problem for future generations lies in the hands of designers and engineers, as over 80% of a product’s lifelong environmental impact is determined during the design phase.
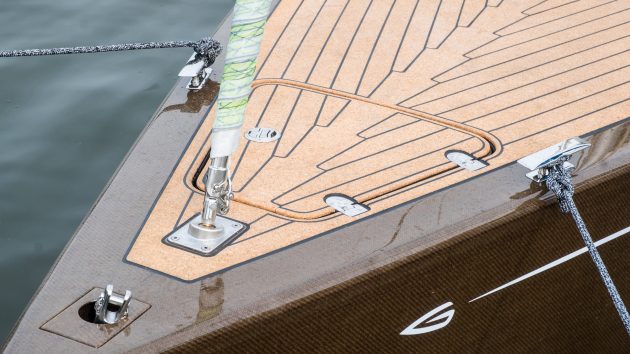
German yard Greenboats has started building yachts from a flax based laminate
New fleet
The new fleet is potentially easier to solve, as it currently exists within the minds of the industry’s designers and engineers, who have the power to solve this problem permanently. The key lies in the marine industry’s ability to transition to circular models of operation. Much of this will be driven by coming legislation. EPR and the addition of ‘digital product passports’ will require manufacturers to not only take their product back at EOL but also provide full transparency and traceability of a product’s impact across its entire lifespan.
All manufacturers will have to change their business models and design production processes to ensure they extract maximum value from the product at EOL. With the increasing availability of bio-based materials, recyclable resin systems and novel ownership models being developed every day, the future looks bright for boatbuilding. Whether the current industry’s heavy hitters choose to take notice and alter their path, however, remains to be seen.
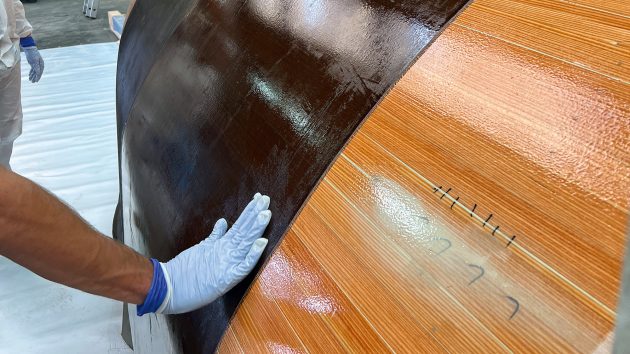
Laminating a flax-based panel
Flax future
Bio-based materials and natural fibres offer multiple benefits across the life cycle of a vessel. They come from renewable feedstocks that can be regrown on an annual basis and have low global warming potential as they produce fewer greenhouse gas emissions during production.
Plant-based fibres also sequester carbon during growth and lock this carbon into the structure for the life of the product. The calorific value of flax-based structures is far greater than GRP as both the fibre and resin get burnt, increasing energy recovery.
Flax, if used with a bio-based resin system, will also naturally biodegrade over time, returning the stored carbon to the short-term carbon cycle.
German boatbuilder Greenboats has developed a novel concept utilising flax-based laminate panels. It produces interior panels, doors and bulkheads from flax which has NFC (near field communication) chips embedded into the laminate structure to show the user or recycler the complete material content and process for recycling, including strain gauges and temperature sensors, so they know what level of stress a panel has experienced across its 30-year lifespan.
Design for Disassembly
Another core concept boatbuilders might embrace is ‘design for disassembly’. Lots of work is being done to create reversible bonding joints using thermally expanding graphite particles, for instance, to make splitting bonded composite panels possible.
Or even simpler, looking at using traditional panel designs rather than highly complex moulded shapes so the deconstruction at EOL is straightforward, with the resultant panels capable of being reused in new structures.
Enjoyed reading this?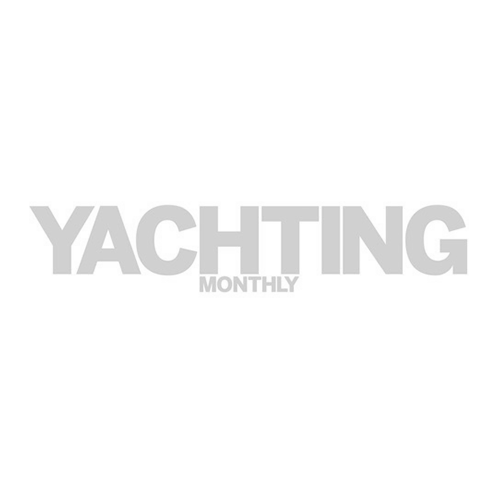
A subscription to Yachting Monthly magazine costs around 40% less than the cover price.
Print and digital editions are available through Magazines Direct – where you can also find the latest deals.
YM is packed with information to help you get the most from your time on the water.
-
-
- Take your seamanship to the next level with tips, advice and skills from our experts
- Impartial in-depth reviews of the latest yachts and equipment
- Cruising guides to help you reach those dream destinations
-
Follow us on Facebook, Twitter and Instagram.